Micro-Manufacturing
Cultivating Industrial Reintegration Within Post Industrial Cities
December 2020
research conducted under Prof. Alejandro Zaera-Polo
Context
For centuries, industrialized cities have operated as hubs for the commercial production and sale of precision manufactured goods. However, over the last fifty years, many of these urban centers have transitioned towards offshore operations that employ widespread automation of linear manufacturing processes over the last fifty years due to technological and economic influences. To fill the void posed by the recent decline of urban manufacturing, cities have focused on developing post-industrial service sector industries. However, recent studies have highlighted that without a substantive manufacturing sector, post-industrial cities are ill-equipped to address emerging economic and environmental concerns of urban self-sufficiency & sustainability, growing employment gaps, and service sector oversaturation.
Micromanufacturing
While traditional models of centralized manufacturing are both too costly and environmentally disruptive to be effectively reintegrated into post-industrial cities, emergent micromanufacturing technologies and the rise of decentralized modes of industrial-scale production indicate a possibility for new forms of discreet urban manufacturing. This can offer a plethora of benefits to post-industrial economies, employing economically vulnerable socio-demographic groups, more efficient usage of materials, and acting as a catalyst and support for new service sector industries.
This paper will conduct a comprehensive examination of two distinct manufacturing trends. The rise and fall of centralized production and company towns and the emergence of decentralized micro manufacturing communities. Drawing from the conclusions in this research, this paper will propose a theoretical framework for the effective reintegration of manufacturing within post-industrial cities. This framework will focus on discerning:
Section 01: A Brief History of Industrial Manufacturing
For centuries, industrialized cities have operated as hubs for the commercial production and sale of precision manufactured goods. However, over the last fifty years, many of these urban centers have transitioned towards offshore operations that employ widespread automation of linear manufacturing processes over the last fifty years due to technological and economic influences. To fill the void posed by the recent decline of urban manufacturing, cities have focused on developing post-industrial service sector industries. However, recent studies have highlighted that without a substantive manufacturing sector, post-industrial cities are ill-equipped to address emerging economic and environmental concerns of urban self-sufficiency & sustainability, growing employment gaps, and service sector oversaturation.
Micromanufacturing
While traditional models of centralized manufacturing are both too costly and environmentally disruptive to be effectively reintegrated into post-industrial cities, emergent micromanufacturing technologies and the rise of decentralized modes of industrial-scale production indicate a possibility for new forms of discreet urban manufacturing. This can offer a plethora of benefits to post-industrial economies, employing economically vulnerable socio-demographic groups, more efficient usage of materials, and acting as a catalyst and support for new service sector industries.
This paper will conduct a comprehensive examination of two distinct manufacturing trends. The rise and fall of centralized production and company towns and the emergence of decentralized micro manufacturing communities. Drawing from the conclusions in this research, this paper will propose a theoretical framework for the effective reintegration of manufacturing within post-industrial cities. This framework will focus on discerning:
- What technologies are suitable for the 21st-century urban industry
- The opportunities and limitations of micro-manufacturing
- The methods through which micro manufacturing can integrate within cities, at urban and structural scales
Section 01: A Brief History of Industrial Manufacturing
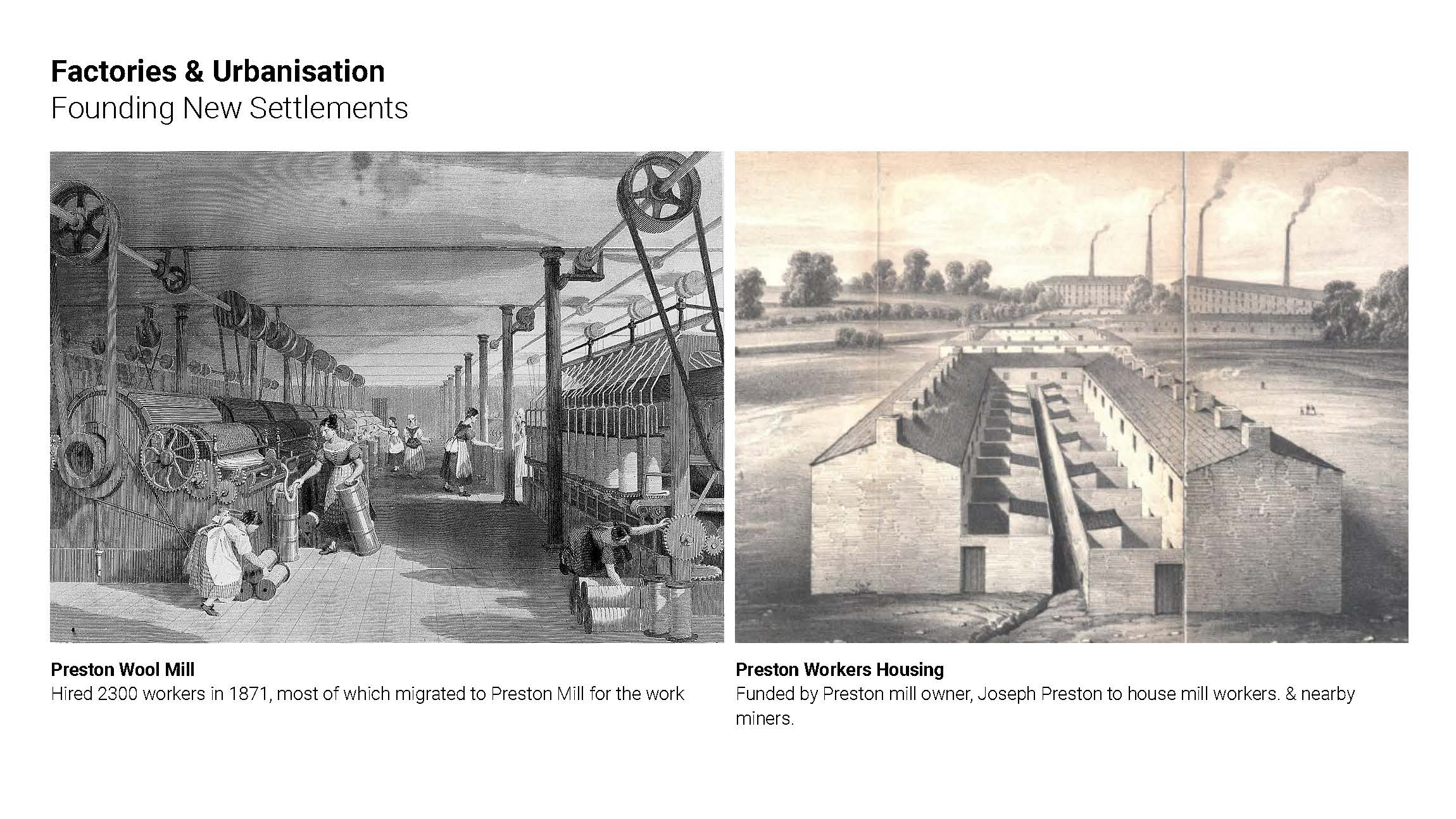

The Rise of the 'Industrial City'
The industrial revolution, widely considered to have originated in the United Kingdom in the mid 18th Century, signified a turning point in history in which agrarian and handicraft economies transitioned rapidly to rely on mechanized production. This economic transformation revised the dominant modes of production and drastically altered the structure of urban settlements and societies that developed therein.
The most pervasive urban influence of industrialization is widely considered to be the foundation of the 'industrial city.' When discussing industrial cities, it is essential to address their unique identifier in that they are new, not only in that most of them were the product of urban growth in the last 200 years, but rather that they had rarely been places of settlement before their rapid establishment. Manchester, widely accepted as the 'first industrial city,' was described by Daniel Defoe in 1727 as a "mere village." Similarly, other heavily industrialized areas in Great Britain and the US were oftentimes wasteland or farmland up until the mid 18th Century. The newness of the industrial city provided industrial developers a unique opportunity, with minimal existing vested interests and cheap land costs affording companies minimal expenses and regulations to test and develop experimental, massive, and often dangerous factories. These factories were used to conduct either light or heavy manufacturing. Heavy manufacturing is engaged in the mechanical, physical, or chemical transformation of materials, substances, or components into new products, frequently producing significant quantities of pollutants and harmful by-products. Light manufacturing is engaged in the transformation of partially processed materials or components into complex assemblies. Both types of manufacturing require significant amounts of labor on-site and complex logistical supply chains to ensure constant and efficient production of goods. Industrial cities were thereby usually established along new or preexisting trade lines like railways and ports, and eventually highways and airports to ensure quick access to raw materials and workers. The high demand for labor, and the comparatively high earnings offered in early industrial factories relative to rural farms, sparked an influx of economic migration towards newly industrialized areas, creating rapidly growing settlements nucleated around factory complexes. By the end of the 18th Century, many of the newly established industrial towns were more extensive and growing at a far faster rate than their pre-industrial counterparts.
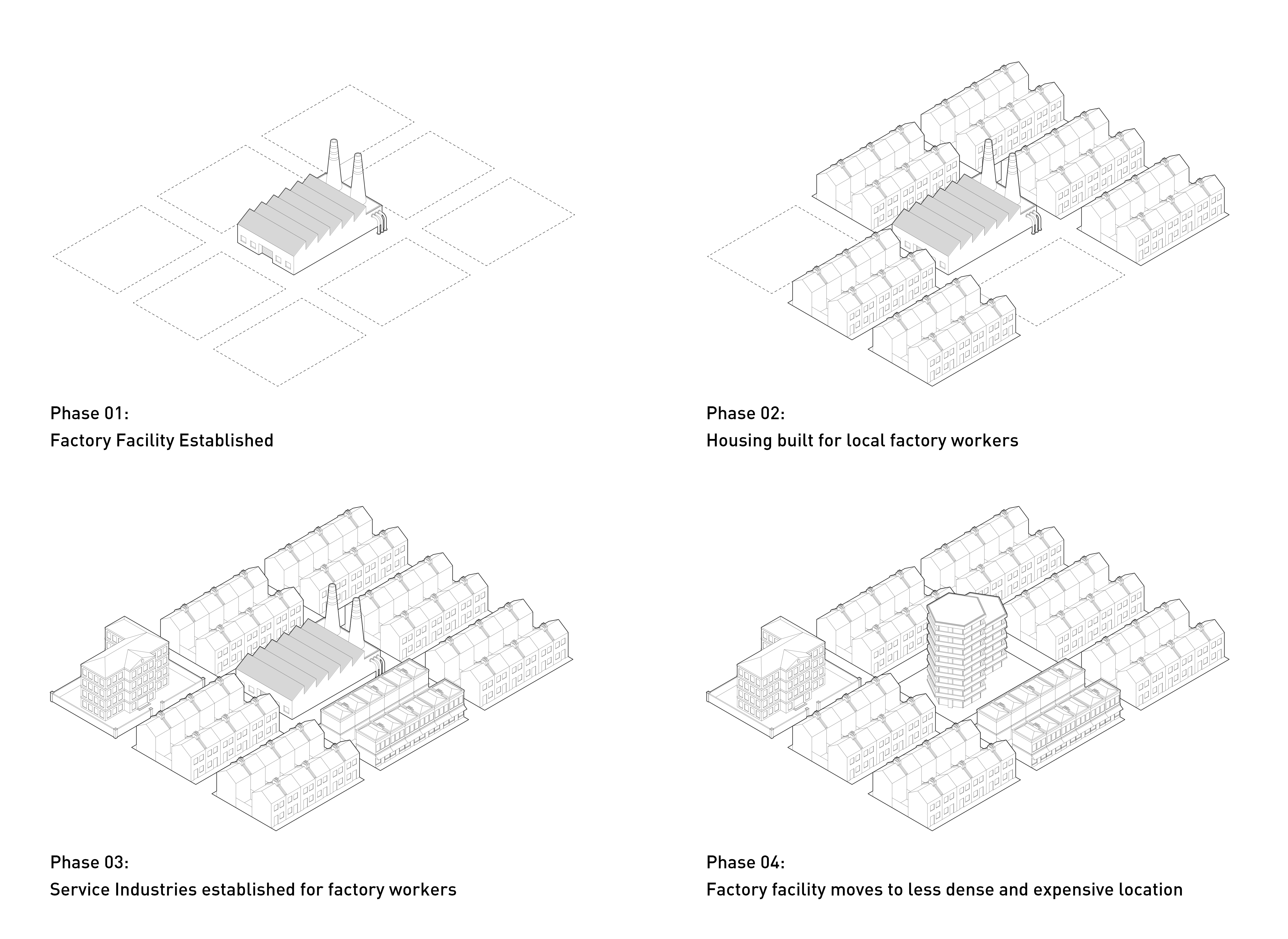
The type of labor required in industrial cities was essential to their meteoric success. With the rise of complex machinery, many traditionally labor-intensive or complex processes were extensively streamlined. Intricate and complex weaving could now be completed quickly and at great precision using mechanized looms. Similarly, complex metal assemblies could have all their components precision-milled or cast en masse in vast machining halls. This allowed types of labor usually reserved for artisans to be reassigned to comparatively unskilled workers, who primarily focused on maintaining mechanical operations and simple assembly tasks. This made industrial cities appealing to less wealthy and less-educated workers, as the labor required had minimal barriers to entry. The appeal of industrialized manufacturing only grew further following the implementation of 'Scientific Management' by Frederick Winslow Taylor at the end of the 19th Century, which essentially reorganized complex manufacturing steps into repeatable and straightforward, linear processes.

While industrial cities were often incredibly polluted and crowded, the continued growth of residential districts around factory complexes stimulated new service industries to cater to the burgeoning industrial workforce. This, in turn, created new waves of affluence within industrial cities [fig. 3]. Over time, as land costs and labor wages continued to increase in industrial cities, many factories were eventually too expensive to operate near the city center and had to re-establish themselves on the urban periphery. This cyclical pattern of factory migration to less densely developed land fueled the continued expansion of industrial cities for much of the 19th and early 20th Centuries.
Globalization and Offshoring
The first signs of decline for industrial cities took hold in the latter half of the 20th Century. By this period, almost all factories had adopted Taylor's scientific management strategies and produced goods through optimized linear processes. Automobiles could be assembled on linear tracks in which teams of workers generally assembled distinct components of the vehicle, one after the other, until a completed vehicle was produced at the end of the assembly line. The costs limiting production for most factories at this point were labor costs, which had been steadily increasing throughout most of the 19th and early 20th Centuries. Up until this point, international production was primarily prohibited due to logistical challenges in operating complex manufacturing across large geographic areas. For a factory to operate efficiently, it traditionally needed to be located close to its essential resource supplies. Cotton mills operated best near pastoral land, and iron processing plants were best located near iron deposits. The expenses incurred in long-distance transportation of resources had indirectly fostered an industrial regionalism, in which local geographies determined what could be manufactured in specific locations.
However, advances in transit during the 20th Century, like increased shipping networks, highways, and air travel, had significantly reduced the logistical costs associated with globally distributed production. Iron could now be mined in Australia, where it is more plentiful and cheaper to extract, processed into automotive parts in Asia where labor is cheap, and assembled in America close to the automotive market [Fig.5]. The economic advantages of the global distribution of industrial production resulted in many manufacturers developing offshore production facilities or subcontracting many of their heavy manufacturing processes to foreign businesses. In doing so, the cycle of industrial urban city growth in older industrialized economies was significantly dampened, while new industrial economies emerged overseas.
The Factory Exodus & Automation
While offshoring did function to hinder the continued growth of industrial cities, it has only accounted for approximately 30% of the decline in manufacturing employment in the US and Europe. The more pervasive cause of industrial employment decline is now widely considered to be the robotic automation of linear production processes. While early machinery employed in factories lacked complexity and still relied heavily on personnel to maintain and operate them, modern industrial equipment can now independently execute many of the more straightforward tasks traditionally assigned to unskilled factory workers. Notably, robotic process automation (RPA) is now utilized to expedite the production of complex assemblies like automobiles, computers, and mobile phones, due to their ability to execute repetitive tasks efficiently and with extreme precision, without the need for a salary. This has had the unusual effect of increasing manufacturing productivity while simultaneously decreasing percentage employment in the manufacturing sector in Europe, the US, and Japan over the past 20 years [Fig.8.2]. Assembly lines that used to employ hundreds of welders and mechanics can now operate effectively with only a handful of robotic technicians [Fig.6]. Furthermore, along with the rapid growth of the robotics industry sector, robots are liable to continue offsetting evermore complex labor tasks within modern factories.
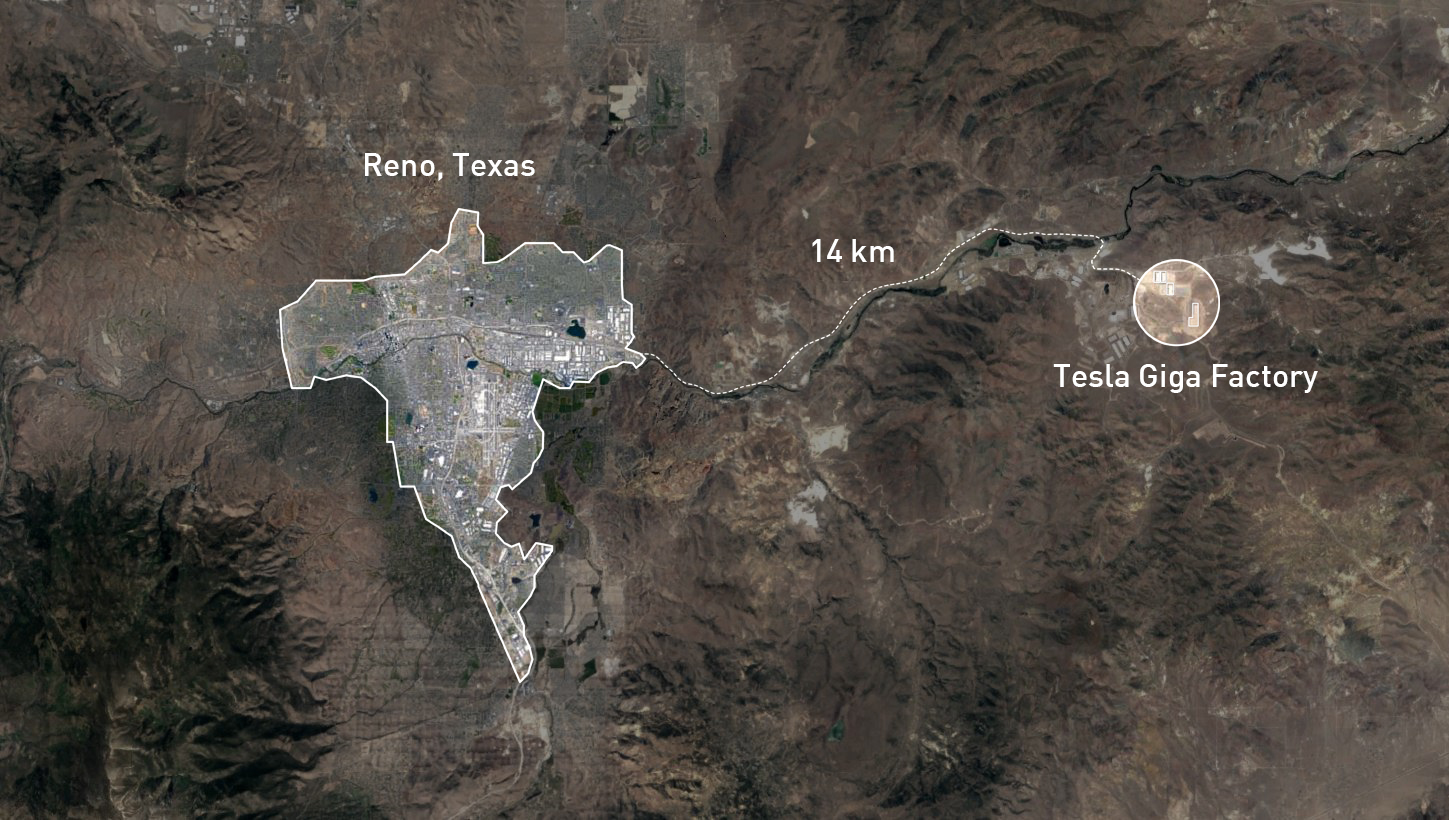
With centralized factory labor becoming increasingly automated, and with the world becoming ever more connected with high-speed infrastructure, many factories are no longer tied to requiring a mostly unskilled workforce in close proximity to operate effectively. This has prompted the production of new factories far to the periphery of industrial cities. The gigafactory one, for example, is located over 20 miles from the nearest city, Reno, primarily because of the affordable land values, taxes, and rent associated with establishing such an expansive factory in the Nevada Desert instead of an urban center.
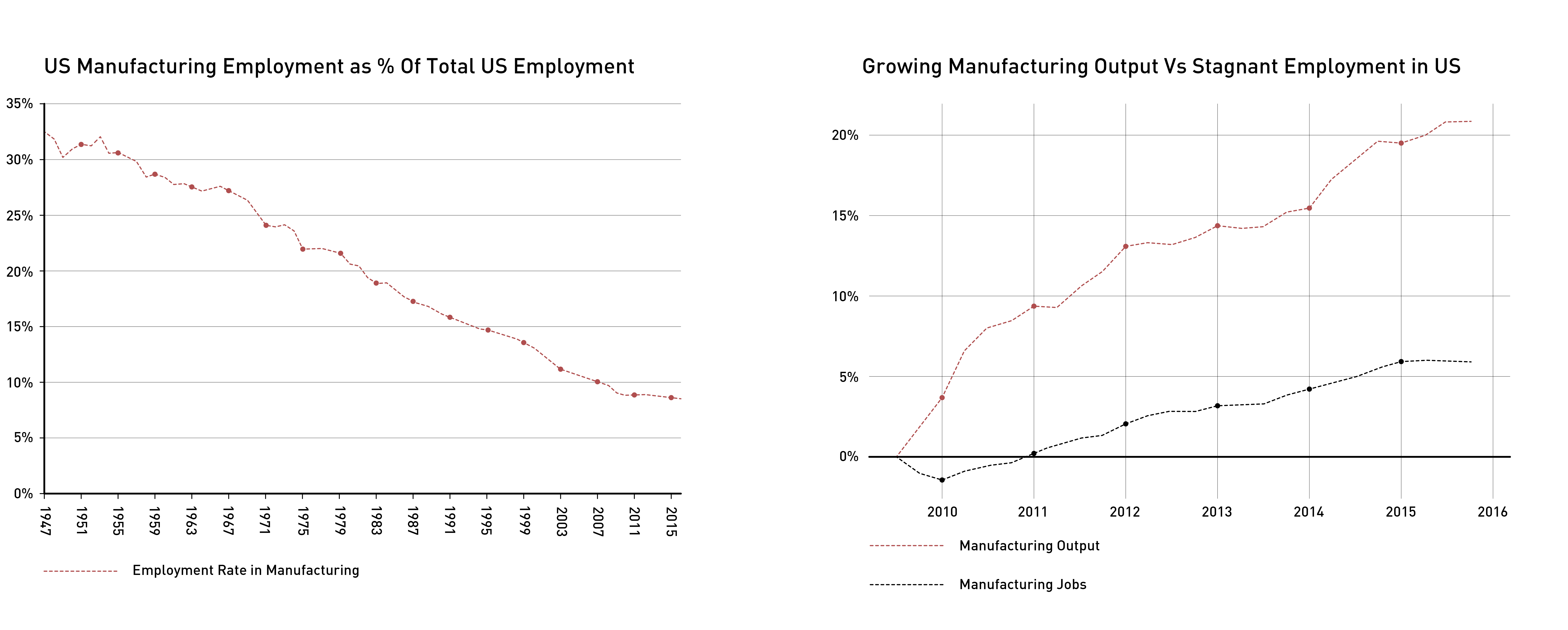
Conclusions
It would be incorrect to state that manufacturing in post-industrial economies is in decline. Indeed, with the rise of automated labor, it is likely that factories will begin to operate more domestically instead of offshoring for competitive labor costs and will continue to increase in productivity and efficiency [Fig.8.2]. However, with a dwindling reliance on human labor and the comparative affordability of establishing rural operations, industrial cities will likely continue to decline economically if reliant on traditional modes of industrial growth.
Section 02: Decentralised Modes Of Production
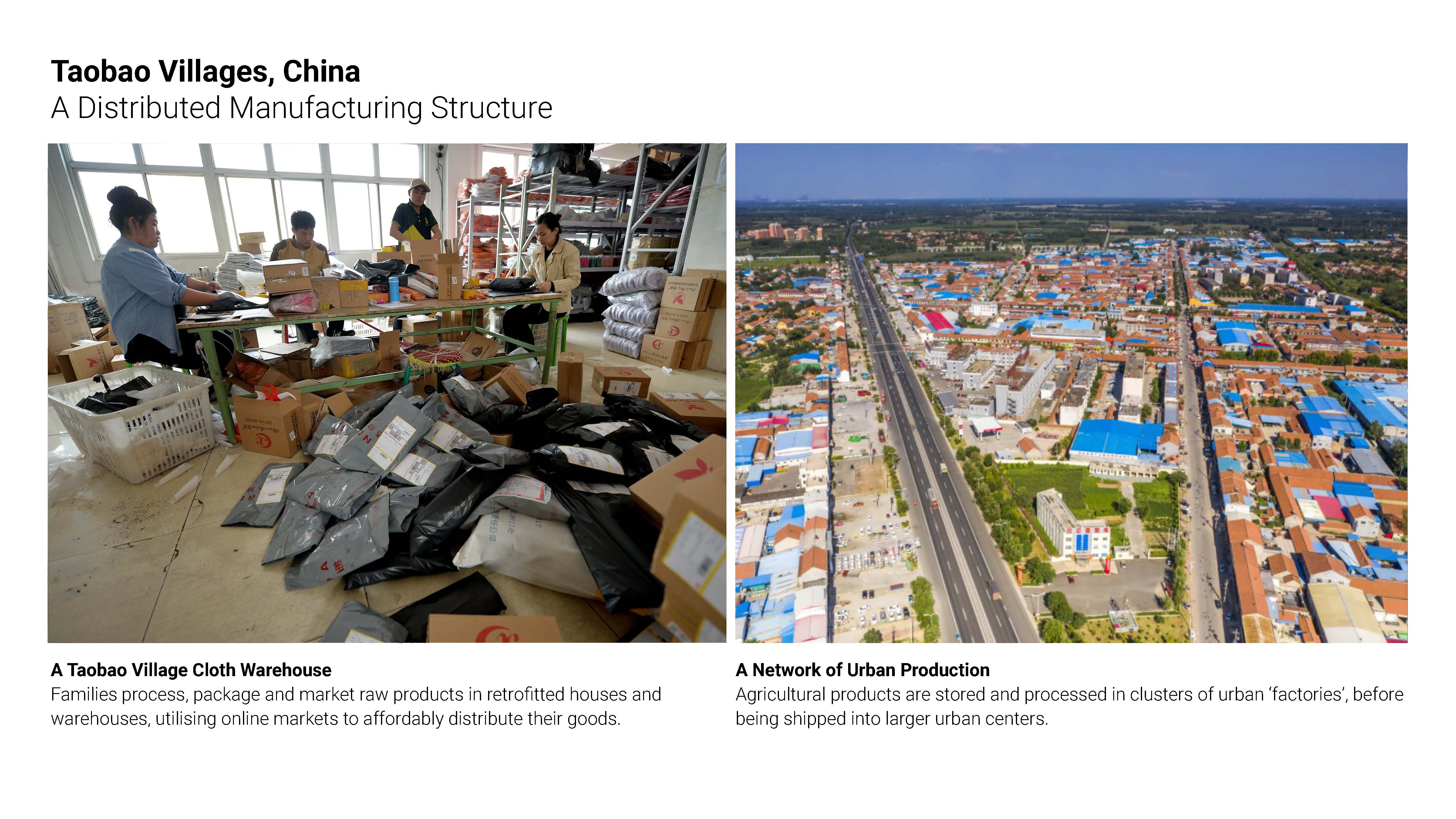
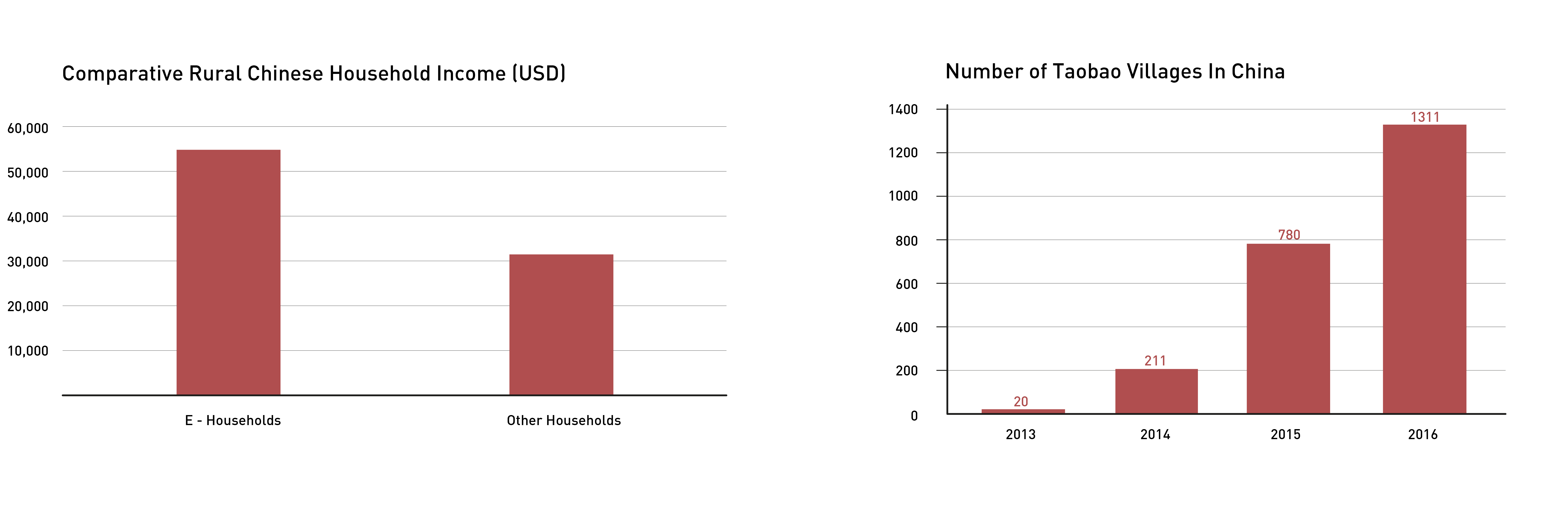
Taobao Villages
While centralized factory operations no longer function as the drivers of urban growth & wealth creation that they once were, new modes of decentralized urban production are both on the rise and fueling new waves of urban expansion and technological innovation. One such wave of distributed production is the emergence and proliferation of Taobao villages in rural China.
AliResearch defines a Taobao village as a settlement containing over 100 e-commerce businesses, with at least 10 percent of all households being directly involved in e-commerce, and with annual e-commerce transactions exceeding a value of 10 million yuan. Similar to traditional industrial settlements, Taobao villages both came into existence exceptionally rapidly and developed from small agricultural communities. The first recorded Taobao village was established in 2009; however, due to their extreme production efficacy, that number had grown to over 4000 settlements by 2019 [Fig.10.2], with Taobao villages cumulatively being responsible for producing over 1.34 Trillion RMB in e-commerce goods annually. The key to the meteoric success and growth of Taobao villages is tied to unconventional approaches to the networked distribution of labor and online sale of goods.
Before their conversion to e-commerce market hubs, many rural Chinese villages were already involved in agrarian production and handicraft manufacturing, converting raw agricultural produce like wool and timber into clothing and furniture items. Traditionally, these villages were reasonably low density and operated via brokers to transport and sell small quantities of their goods in larger urban centers. However, as access to online marketplaces like Taobao and Alibaba and transit links to rural settlements improved, these agrarian communities rapidly transitioned from physical to digital commerce. With platforms like Alibaba and Taobao handling the logistical challenges of transporting goods to consumers, this enabled these agrarian communities to expand their production operations [Fig.11], converting their village homes into production centers and retrofitting their housing into storage warehouses for their products. Furthermore, with smaller transportation costs, greater exposure online, and fewer broker dealings, each village household received a more significant profit share for goods sold, increasing villagers' net income beyond that of urban families [Fig.10.1]. This triggered waves of economic migration from larger urban centers to countryside settlements, which further accelerated the production of new Taobao Villages. Through the clustering of specialized urban producers, vast quantities of specific products could be produced from a network of small facilities rather than through a centralized one. Lumber specialized Taobao Villages could produce thousands of wooden bed items through a collaboration of a cluster of specialized wood manufacturers, whereas vast quantities of wool could be processed into various clothing items in a pastoral Taobao cluster. The vast majority of Taobao products can be categorized into either raw agricultural produce, like cotton, wool, fruit, or handicraft items like furniture or clothing items. By leveraging either the craft or unprocessed quality of the goods produced, much of what is being made in Taobao Villages does not conflict with linear production processes that are easier to automate. In doing so, Taobao villages have managed to thrive in a country that is already heavily reliant on automated centralized production.

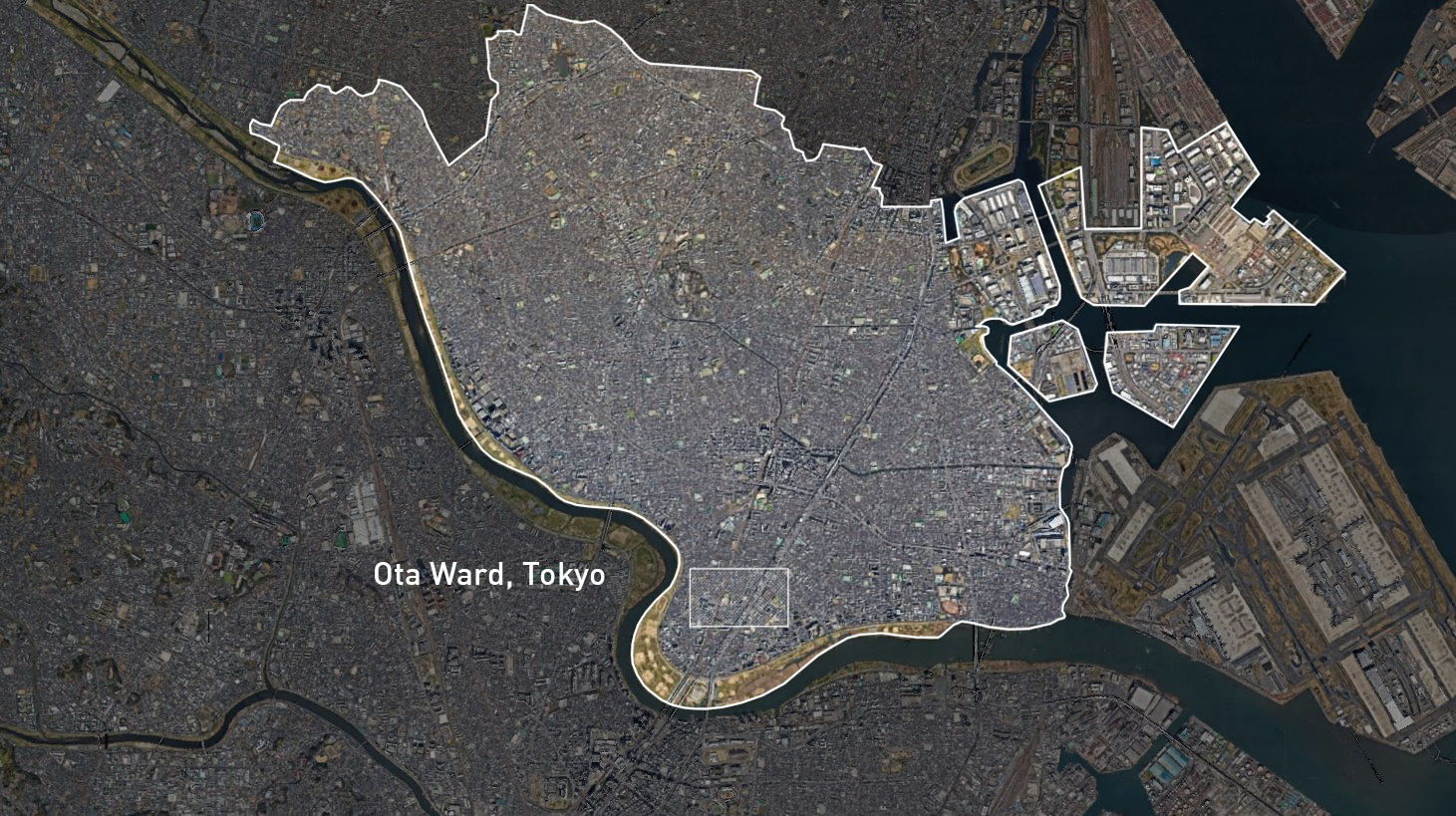
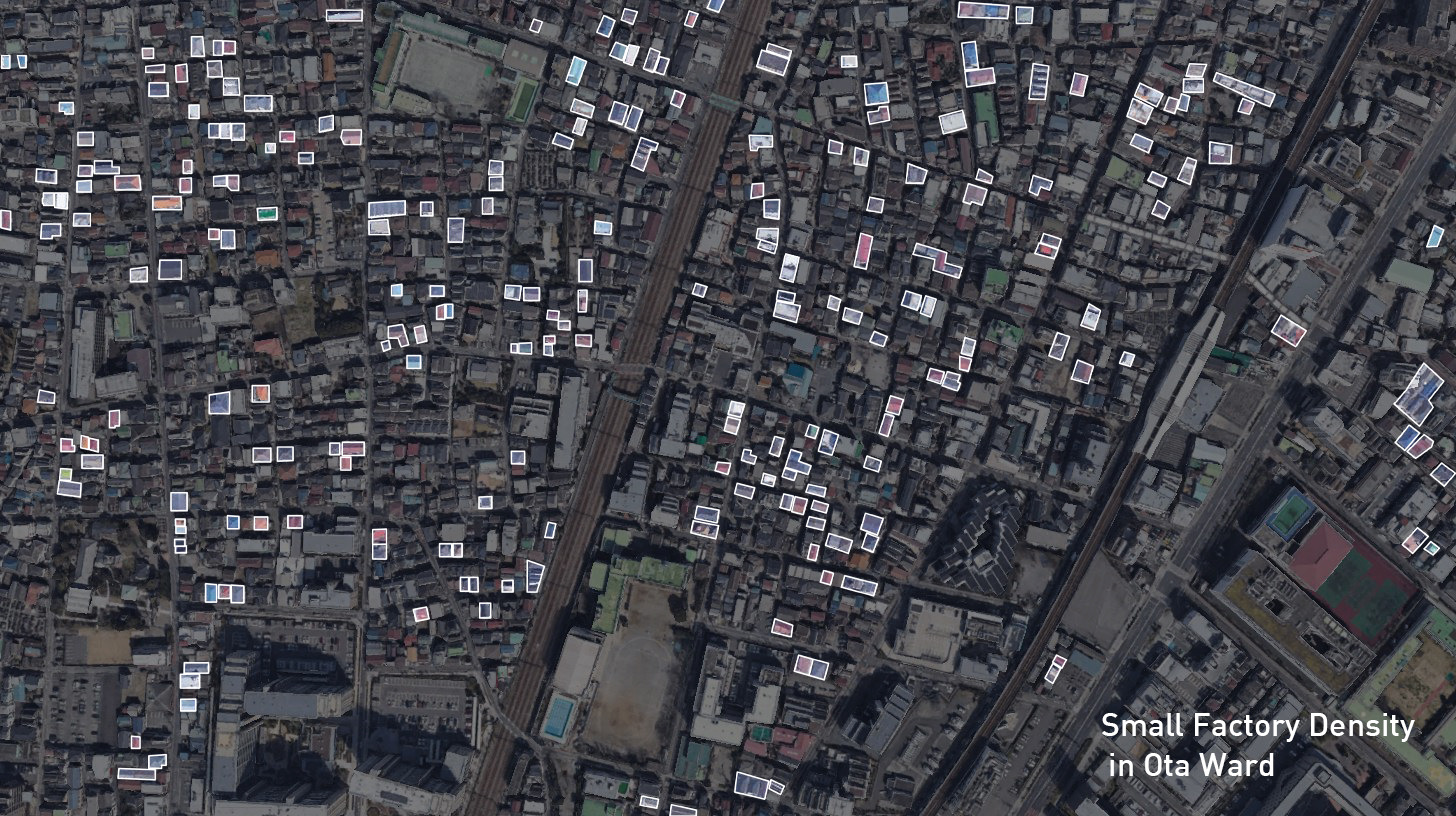
There are, however, limitations to the widespread application of a distributed e-commerce production system as advocated by the Taobao village model. Primarily, there are cultural conditions endemic to rural China that have led to their widespread success, which may be hard to replicate elsewhere. For example, much of rural China was engaged in large scale handicraft manufacturing prior to the formation of Taobao villages. The growth of Taobao villages is merely reflective of these communities' greater empowerment to market their products directly to consumers. Furthermore, the production methods in rural settlements have remained somewhat unchanged following their shift to e-commerce marketing. Therefore, the early proliferation of Taobao Villages was dependent on its preexisting agrarian and handicraft manufacturing culture, which may not be present in other post-industrial economies. Nonetheless, the unprecedented growth of Taobao Villages serves to showcase a return to regional manufacturing communities and the power of advanced logistics and e-commerce to coordinate clusters of small communities for large scale production.
Another type of decentralized manufacturing community that has undergone a recent surge in growth is found within Japan's 'small factory' districts. The Japanese municipal government defines small Factories as factory operations that employ less than 30 workers, though the vast majority of businesses that fall under the small factory criteria generally employ less than 10. Across Japan, over 45,000 of these 'small factory' operations are used to subcontract precision machined components that are either too precise or customized to be produced in mass production facilities, employing over 90% of Japan's manufacturing workforce. Unusually, despite their use of industrial machinery, small factory districts are mostly residential, with individual operations being embedded within housing units and small warehouses. The most densely populated small factory cluster is Ota Ward in Tokyo, home to over 4000 small factory operations.
The origins of small factory districts stem from the chaos following World War II, wherein much of Japan's factory districts & housing had been destroyed by allied forces, and demand for military rearmament was at an all-time high. Ota Ward was in ruins following the war, and the government had little means to regulate the district's redevelopment, resulting in the area developing autonomously from the rest of Tokyo in a way that blurred the boundaries of 'public and private' and 'work and life.' Urban workshops became a key feature of Ota, in which industrial machining operations were conducted on the ground floor using recovered wartime precision tools, while families were housed on the second floor of the same building. These urban workshops were initially used to kickstart industrial production of military arms following World War II, giving residents and slum dwellers much-needed employment. However, Japan's economy grew, the skill, number, and specialization of the Urban workshops continued to grow and began to be used for all manner of precision metal manufacturing, from aerospace to micro tooling. This further spurred Ota Ward's small factory community's growth until it peaked in the 1980s, in which it comprised 9000 small factory operations.
Unlike the Taobao Village success story, small factory districts like Ota Ward could not easily coexist with the cost-effectiveness of automated factory production. Between 1990 and 2010, Ota Ward underwent a gradual decline in small factory operations, triggered by Japan's housing crisis and sustained by the shift towards automated manufacturing in the precision machining industry. During this period, much of the general manufacturing contracts for Japanese companies were given to automated production facilities. Urban workshops were able to carve a niche for themselves through the machining of small batch custom components, though this was not enough to sustain the vast number of operations that had set up shop in Ota Ward, resulting in the number of small factories between 1990 and 2010 to decline to less than 3500.
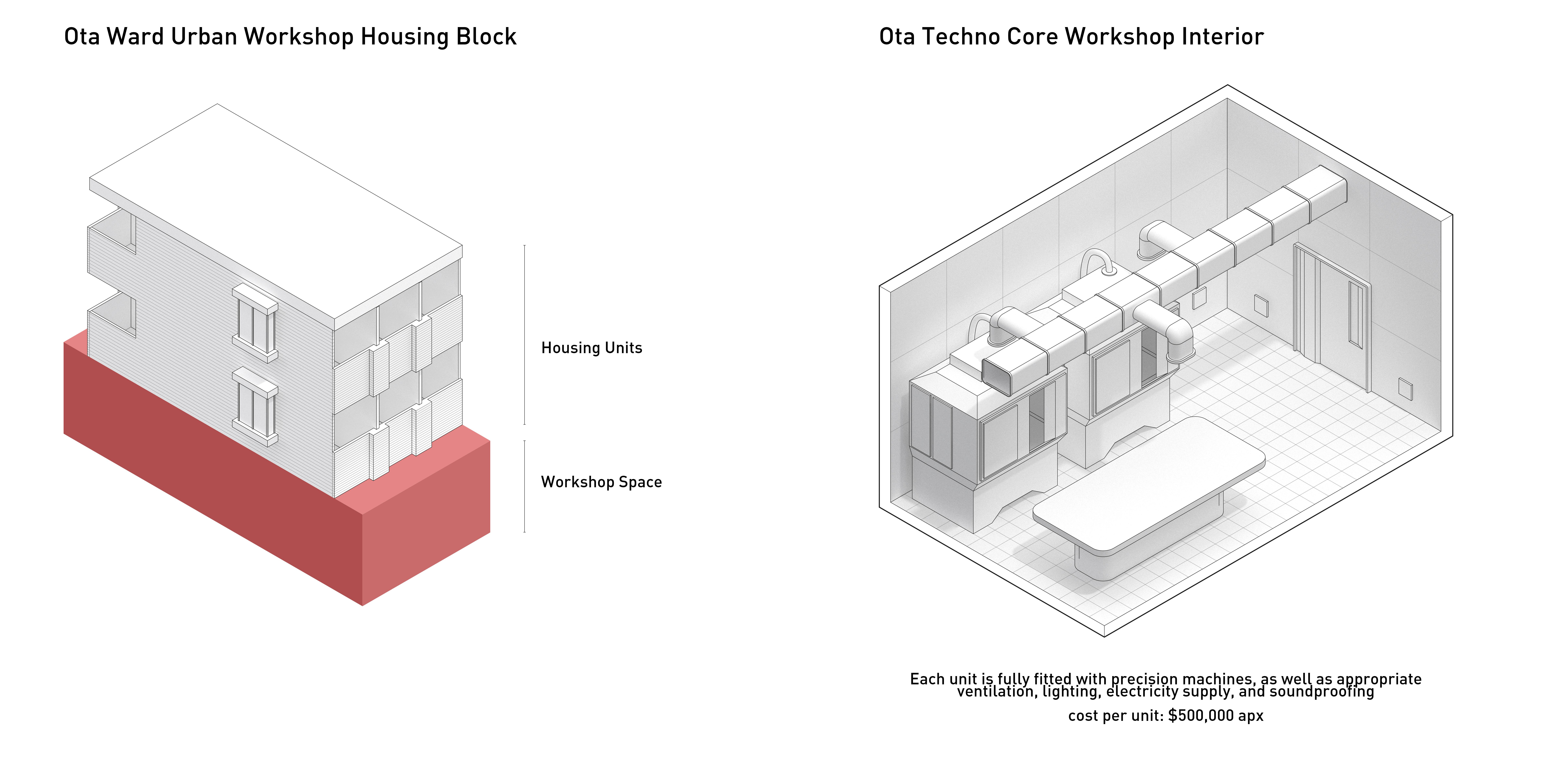

However, over the last decade, there has been a resurgence of interest in Ota Ward's manufacturing sector. The district is now a key location for experimental high-tech prototyping and development. This is because of "Nakama Mawashi" (literally meaning passing something around to friends). The proximity of different specialist machining centers, with owners often being neighbors and close friends, affords the area a unique collaborative community where groups of machinists assist one another in completing projects. This collaboration ethos allows for abstract concept designs to be rapidly developed into concrete prototypes, which has made the district a beacon for technological innovation. This has led to increased corporate and governmental involvement with the district since 2010, with government-funded urban workshops like the Ota Techno Core being developed to encourage new generations of small factory owners. Housing units like the Ota Techno Core follow the same structure of traditional urban workshops, with a machine shop at ground level and housing on the upper floors [Fig. 14.1]. However, the design of each workshop integrates the extensive electricity and ventilation systems required to house modern machinery and are soundproofed to minimize noise pollution [Fig 14.2]. In doing so, new urban workshops are more discreet than their impromptu counterparts and are more appealing to new generations of machinists. These government and commercially sponsored urban workshops now comprise the additional 1000 small factory operations that have arisen in Ota Ward since 2010. The resurgence of urban machining clusters within a post-industrial city like Tokyo indicates the potential of collaborative and complementary manufacturing communities, not as a production powerhouse, but instead a launchpad for high tech enterprises and technological innovation.
Micro Factories & Disruptive Technologies
While clusters of urban machinists like the Japanese 'small factories' are experiencing a renewed popularity as hubs for rapid prototyping, their growth is limited due to traditional high-end machining's financial barriers to entry. Conventional machine shops utilize an array of precision processing tools that are incredibly expensive to purchase and maintain. Most of the machinery used currently in the urban workshops of Ota Ward date back to the 1970s and is no longer commercially produced, requiring bespoke components to repair. Younger machinists have to train in the workshops for many years before elderly staff pass on the machines to them as retirement heirlooms. To encourage the new wave of urban workshops, the Japanese government had to fund and supply precision tools within each apartment complex they built, at the cost of approximately $500,000 per housing unit. The recent machining growth in Ota Ward is thereby being artificially accelerated through significant government investment and may not pose an economically sustainable method of reintegrating manufacturing into urban environments.
However, the widespread adoption of compact and affordable precision machining tools may serve to challenge this paradigm. Two of the most effective tools that are now shifting the accessibility of precision machining are 3d printers and CNC Mills [Fig.15]. 3d printing is one of the newest methods of 3d object production methods and depends primarily on fused material deposition (FDM) as a means of sandwiching layers of relatively flat filament layers into complex 3d objects. This process revolutionized manufacturing in 3 ways. Firstly, it builds objects additively and wastes very little material when producing an object, compared to carving out an object from a stock. It can also construct complex 3d objects with multiaxial curvature and nested structures that would otherwise require many different separate machines and processes to create. Finally, it can integrate seamlessly with CAD software, allowing digital models to be rapidly translated into physical prototypes. CNC milling allows for the precision subtractive carving of objects and can rapidly produce carvings translated from digital models; however, with a greater quantity of waste material. However, CNCs generally have larger bed sizes, greater precision tolerances, and can mill from high-density materials like steel and wood that are either challenging or impossible to 3d print. When used in conjunction with one another, these two tools can rapidly fabricate almost any 3d object within their respective bed sizes while requiring minimal post-processing. The construction of 3 axes CNC mills and SLS 3D printers both rely on similar multiaxial movement components for their tool heads, namely spindles, gantries, axial bearings, axial drivers, and precision rails. As these components have become more widely produced, the cost of producing both of these tools has dropped dramatically. Entry-level CNC mills that cost 50,000 USD in 2005 can now be purchased for under 8000 USD. Even more dramatically, entry-level SLS 3d printers are more precise, faster, and more affordable than ever before, with models like the $749 2019 Prusa i3 being able to print approximately five times faster at twice the resolution of a $5000 2010 Makerbot replicator 2. The relative affordability and effectiveness of modern CNC milling and 3D printing equipment have acted to abolish many of the prohibitive costs associated with precision machining, making the industry accessible to hobbyists and smaller enterprises alike.
However, the widespread adoption of compact and affordable precision machining tools may serve to challenge this paradigm. Two of the most effective tools that are now shifting the accessibility of precision machining are 3d printers and CNC Mills [Fig.15]. 3d printing is one of the newest methods of 3d object production methods and depends primarily on fused material deposition (FDM) as a means of sandwiching layers of relatively flat filament layers into complex 3d objects. This process revolutionized manufacturing in 3 ways. Firstly, it builds objects additively and wastes very little material when producing an object, compared to carving out an object from a stock. It can also construct complex 3d objects with multiaxial curvature and nested structures that would otherwise require many different separate machines and processes to create. Finally, it can integrate seamlessly with CAD software, allowing digital models to be rapidly translated into physical prototypes. CNC milling allows for the precision subtractive carving of objects and can rapidly produce carvings translated from digital models; however, with a greater quantity of waste material. However, CNCs generally have larger bed sizes, greater precision tolerances, and can mill from high-density materials like steel and wood that are either challenging or impossible to 3d print. When used in conjunction with one another, these two tools can rapidly fabricate almost any 3d object within their respective bed sizes while requiring minimal post-processing. The construction of 3 axes CNC mills and SLS 3D printers both rely on similar multiaxial movement components for their tool heads, namely spindles, gantries, axial bearings, axial drivers, and precision rails. As these components have become more widely produced, the cost of producing both of these tools has dropped dramatically. Entry-level CNC mills that cost 50,000 USD in 2005 can now be purchased for under 8000 USD. Even more dramatically, entry-level SLS 3d printers are more precise, faster, and more affordable than ever before, with models like the $749 2019 Prusa i3 being able to print approximately five times faster at twice the resolution of a $5000 2010 Makerbot replicator 2. The relative affordability and effectiveness of modern CNC milling and 3D printing equipment have acted to abolish many of the prohibitive costs associated with precision machining, making the industry accessible to hobbyists and smaller enterprises alike.
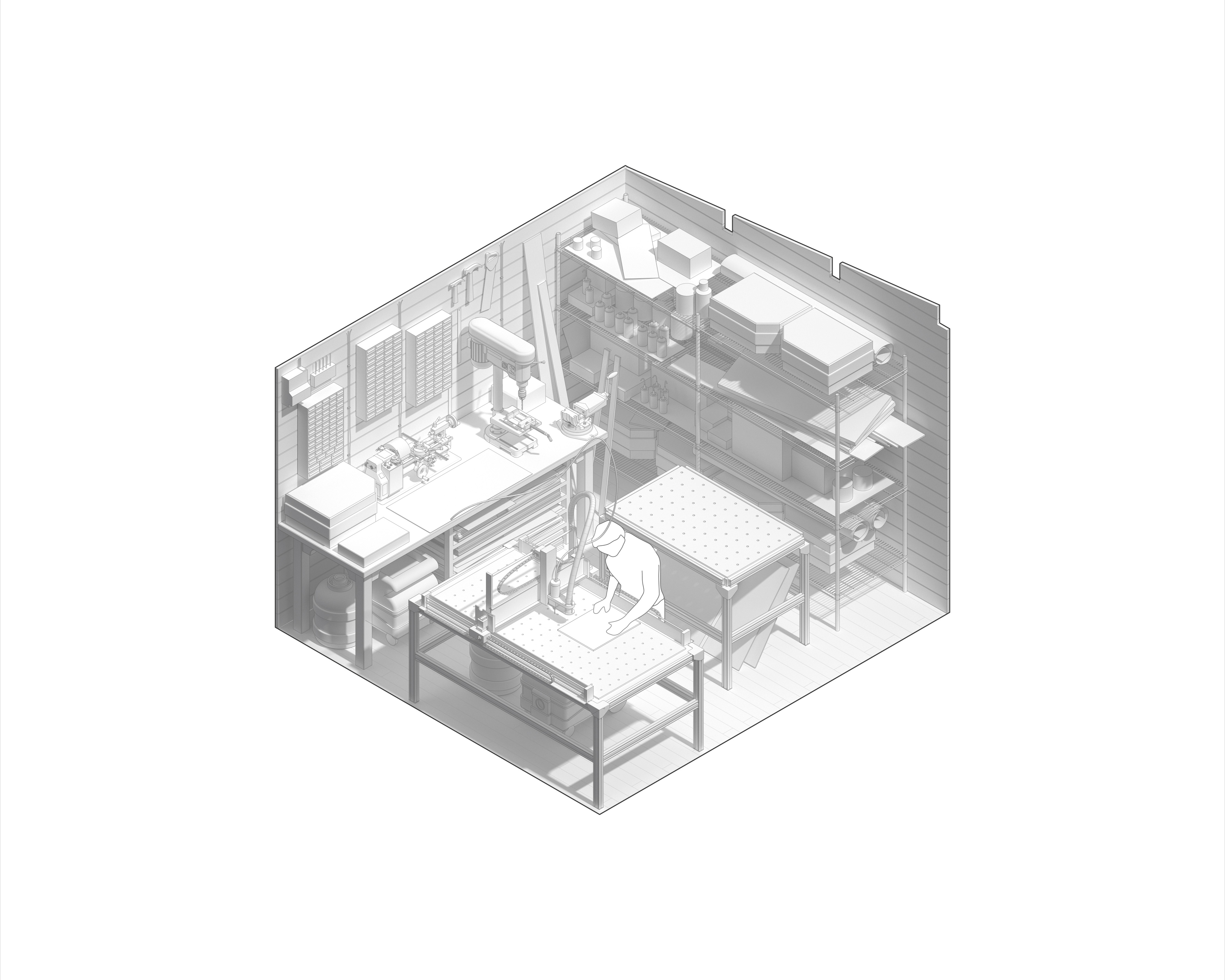
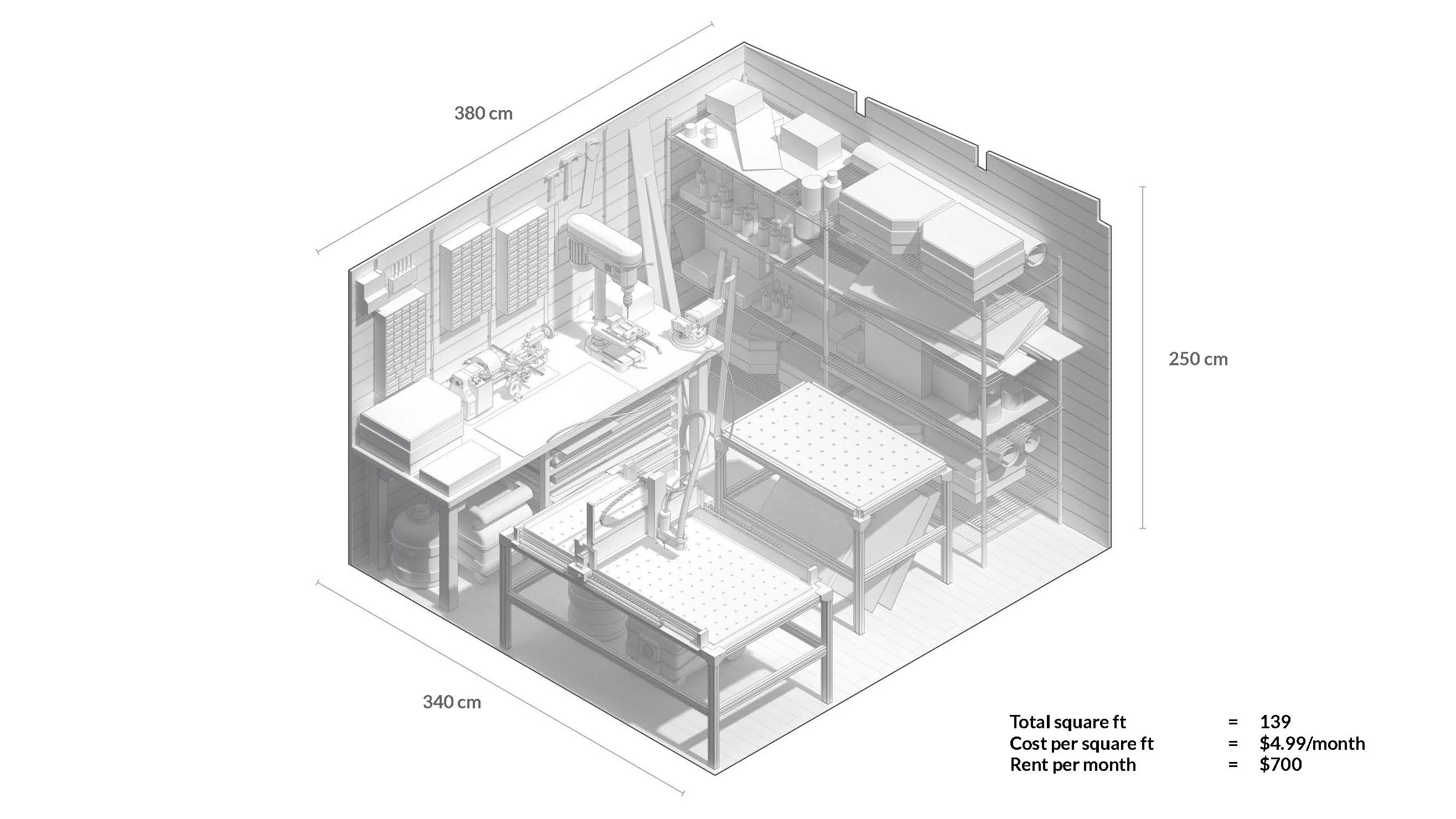

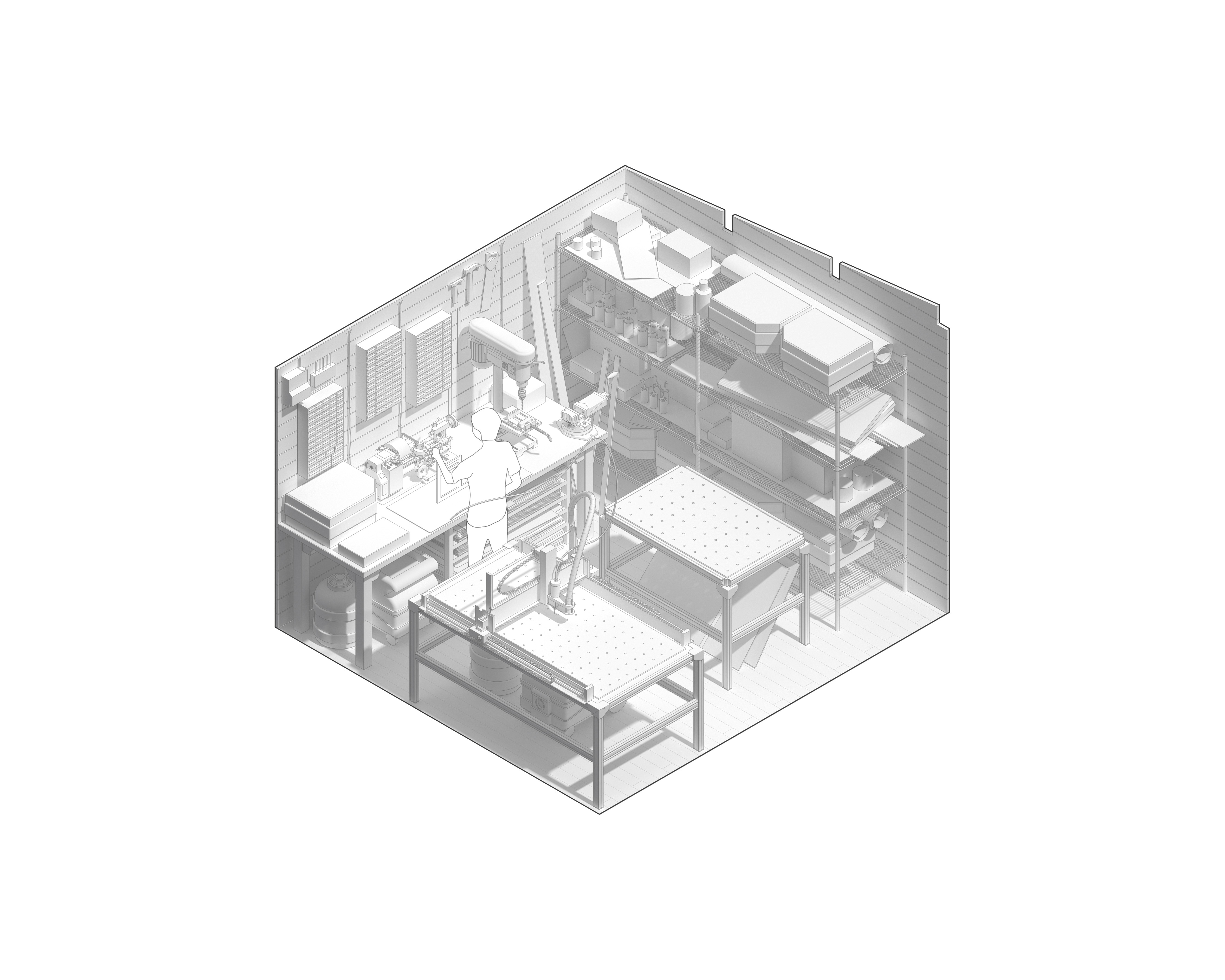
While nascent, the growing accessibility of CNC and 3d printers have propagated the inception of new communities of machining enthusiasts, establishing small micromanufacturing operations that mirror the impromptu developments of the early urban workshops of Ota Ward. These operations usually consist of enthusiasts integrating these industrial machines into their living spaces to locally produce bespoke items, accept small batch machining contracts, or design and prototype components. What differentiates this new community from that of the Japanese small factory community is their lack of dependence on large, expensive equipment, streamlined toolsets, and greater integration of CAD modeling and online marketing in their operations [Fig.16]. This has allowed the micromanufacturing community to develop discreetly within suburban districts, derelict industrial structures, or office spaces, without forming industrial districts or clusters. These dispersed and somewhat isolated operations are now garnering the attention of municipal authorities in post industrial cities, like London, New York, Rotterdam, and Brussels, which are all starting to document the rise of this new wave of dispersed urban manufacturing.
There are, however, challenges that may inhibit the potential growth of these communities. Primarily, the dispersed nature of micromanufacturing operations decreases the opportunity for neighborly collaboration and the cross-pollination of ideas in machining. Secondly, the impromptu locations of many of these micro manufacturing operations are often ill-suited for operational scaling. While a small operation may only need a couple of machines to operate effectively, as the business ages, it will generally increase and refine production, requiring either additional machines or more industrial-scale machinery. This will incur more spatial and ventilation demands, electricity consumption, and noise pollution. To do so may cause many operations to move to more extensive industrial facilities with high rents. This can act to undermine the competitiveness of micro-manufacturing as opposed to centralized operations. Therefore, to optimally foster the growth of micro-manufacturing communities, they must be supported by appropriate urban and housing policies.
There are, however, challenges that may inhibit the potential growth of these communities. Primarily, the dispersed nature of micromanufacturing operations decreases the opportunity for neighborly collaboration and the cross-pollination of ideas in machining. Secondly, the impromptu locations of many of these micro manufacturing operations are often ill-suited for operational scaling. While a small operation may only need a couple of machines to operate effectively, as the business ages, it will generally increase and refine production, requiring either additional machines or more industrial-scale machinery. This will incur more spatial and ventilation demands, electricity consumption, and noise pollution. To do so may cause many operations to move to more extensive industrial facilities with high rents. This can act to undermine the competitiveness of micro-manufacturing as opposed to centralized operations. Therefore, to optimally foster the growth of micro-manufacturing communities, they must be supported by appropriate urban and housing policies.
Section 3: The Micro-Manufacturing Revolution
Urban Maker Clusters
Both Taobao Villages and Japanese 'small factories' have illustrated the efficacy of interconnected but dispersed clusters of manufacturing communities that can lead to extreme economic and urban growth despite automation. However, it is also clear that success in both cases was not achieved entirely organically. The growth of Taobao Villages was dependent on concerted efforts of digital corporations like Alibaba and Taobao to improve rural online marketing literacy in conjunction with the Chinese government's heavy investment in rural highway development. Similarly, Ota Ward's small factory district would likely have continued to decline if not for significant government support in developing mixed workshop/housing initiatives for the next generation of urban machinists. This paper will now suggest a two-part framework aimed at propelling micromanufacturing development within post industrial cities.
Similar to Ota Ward's small factories, micro-factories are ideal operations for rapid prototyping and small-batch production, rather than high production handicrafts like what is offered through Taobao Villages. However, while multiple product development processes can be expedited through "Nakama Mawashi" in districts like Ota Ward, current micro-factory operations elsewhere lack the density, community, and connectivity to operate collaboratively or constructively. To achieve "Nakama Mawashi," micro-factories' dispersed operations will need to be concentrated into clusters of makers [Fig.17]. This can be managed through zoning recalibration to ensure that former industrial land can be affordably reused for new micro-factory operations or through tax incentives to encourage operations to establish themselves in specific places rather than be dispersed. Furthermore, these clusters can be further curated to encourage similar micro-factory or complimentary manufacturing operations to cluster in similar parts of the city, ensuring the optimal potential for cross-pollination and collaboration. In structuring clusters this way, different forms of production can be associated with different city districts, engendering micro-manufacturing regionalism at the scale of the city.
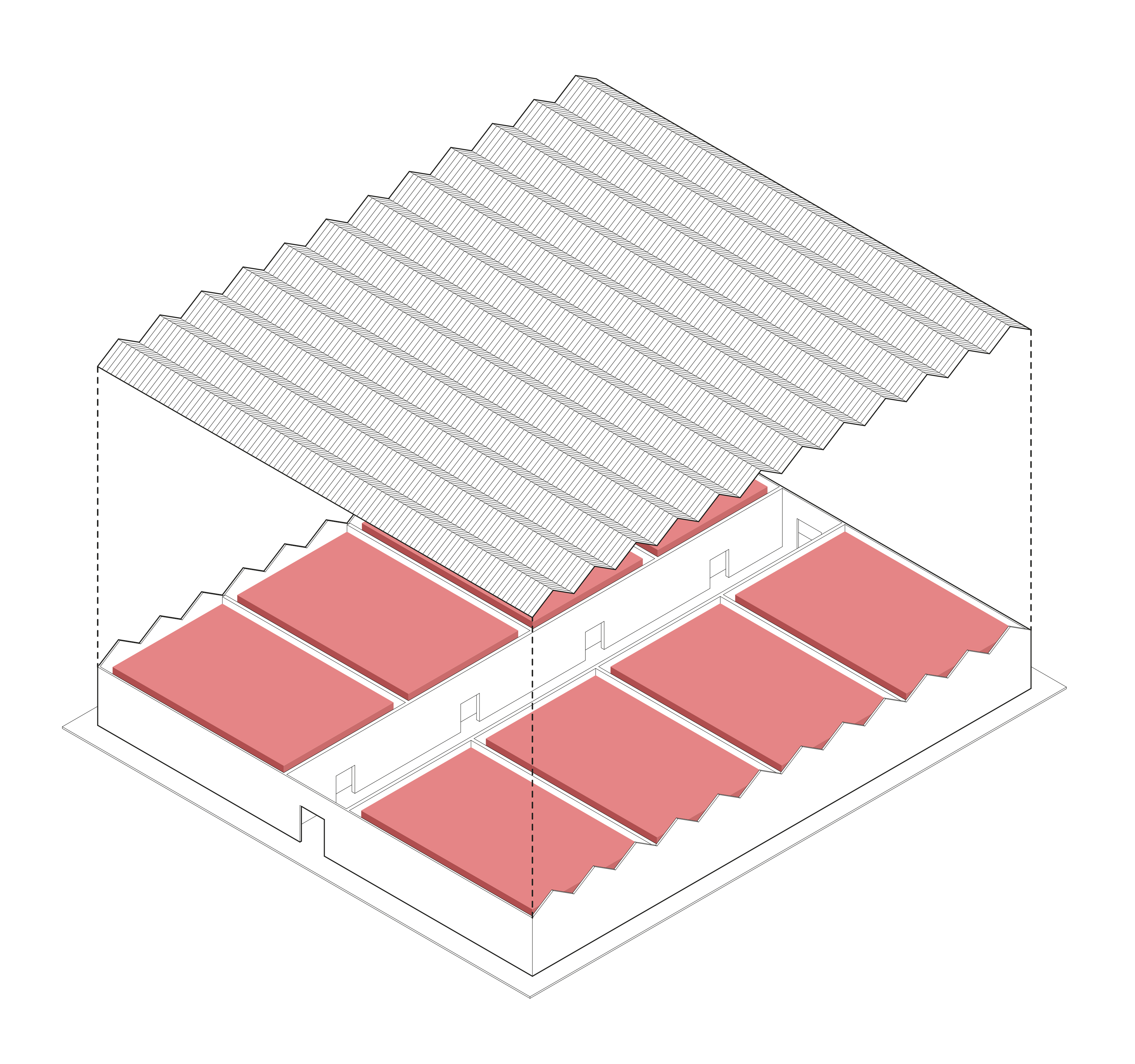
A Flexible Urban Workshop Typology
To tackle the issue of micro-factory scaling & the negative perception of manufacturing in post industrial cities, new types of urban workshop structures should be developed that minimize the harmful by-products of light manufacturing and raise awareness of the presence of the micro-manufacturing industry [Fig.18 & 19]. Machining, even on a small scale, requires large amounts of electricity and potentially produces air and noise pollution, all of which are undesirable for most modern city residents. As most urban structures are not suited for machining, productivity, and scalability for many micro-factory operations are hindered. Learning from projects like the Ota Techno Center, many of the less desirable by-products of micromanufacturing can be mitigated by developing new urban workshops that integrate state of the art soundproofing, electrical, and ventilation systems. However, unlike the urban workshop structures of Ota Ward, the expensive installation of high-end machines would not be required, allowing workshop users to place their machinery within and to customize the workshop space to suit their applications [Fig.19.2]. Finally, to raise awareness and support of the micro-manufacturing sector, this new urban workshop type should be designed to showcase the work undertaken within, so while the industry remains quiet and unobtrusive to nearby residents, it will be noticeable.
It is unlikely that heavy manufacturing processes are ever to return to post industrial cities, at least not in the concentrations present in the early 20th Century. Not only have the increasing scale of mass production factories made their land requirements unsustainable to operate in most cities, but their need for a large locally based human workforce is continuing to decline due to the use of automated technologies. Post-industrial societies have also evolved, with residents getting ever more discontent with the polluting by-products of large scale factory operations. The likely continued exodus of large scale factory operations from the city to the countryside has potentially disastrous consequences for unskilled labor groups that lack qualifications or experience relevant for service sector professions. The potential reintegration of light manufacturing to post-industrial areas through micro-factories may help ameliorate the growing unskilled employment gap, but only to a limited extent.
It should be noted that the use of digitally integrated manufacturing equipment requires very different skill sets to that of linear assembly operations and that many forms of micromanufacturing also require extensive training in digital software. However, these industries still require less skilled labor to support logistics, storage, and less complicated post-processing and assembly tasks essential for efficient productivity. Furthermore, if carefully supported, micro-factories have the potential to act as prototyping launchpads for new technologies, goods, and services, fostering the growth of new companies that could stabilize the currently oversaturated job market. Finally, due to their compact scale and less intensive production techniques, micro-factories can reintegrate urban manufacturing with far fewer toxic by-products, harmful emissions, and reduced levels of disruptive noise pollution. Therefore, this research advocates for governmental and corporate support for the planned cultivation of micro-factory districts and structural typologies to ensure the economic resilience and sustainability of post-industrial cities.
Limitations & Conclusions
It is unlikely that heavy manufacturing processes are ever to return to post industrial cities, at least not in the concentrations present in the early 20th Century. Not only have the increasing scale of mass production factories made their land requirements unsustainable to operate in most cities, but their need for a large locally based human workforce is continuing to decline due to the use of automated technologies. Post-industrial societies have also evolved, with residents getting ever more discontent with the polluting by-products of large scale factory operations. The likely continued exodus of large scale factory operations from the city to the countryside has potentially disastrous consequences for unskilled labor groups that lack qualifications or experience relevant for service sector professions. The potential reintegration of light manufacturing to post-industrial areas through micro-factories may help ameliorate the growing unskilled employment gap, but only to a limited extent.
It should be noted that the use of digitally integrated manufacturing equipment requires very different skill sets to that of linear assembly operations and that many forms of micromanufacturing also require extensive training in digital software. However, these industries still require less skilled labor to support logistics, storage, and less complicated post-processing and assembly tasks essential for efficient productivity. Furthermore, if carefully supported, micro-factories have the potential to act as prototyping launchpads for new technologies, goods, and services, fostering the growth of new companies that could stabilize the currently oversaturated job market. Finally, due to their compact scale and less intensive production techniques, micro-factories can reintegrate urban manufacturing with far fewer toxic by-products, harmful emissions, and reduced levels of disruptive noise pollution. Therefore, this research advocates for governmental and corporate support for the planned cultivation of micro-factory districts and structural typologies to ensure the economic resilience and sustainability of post-industrial cities.

References:
- Robins, Nick, and Ritu Kumar. "Producing, providing, trading: manufacturing industry and sustainable cities." Environment and Urbanization 11, no. 2 (1999): 75-94.
- Mallach, Alan. “Manufacturing May Be Coming Back, But It Won’t Bring Jobs”. Shelterforce. (2013):1-5.
- Sidney Pollard. "Factory Discipline in the Industrial Revolution." The Economic History Review, New Series, 16, no. 2 (1963): 254-71. Accessed December 22, 2020. doi:10.2307/2598639.
- Hoselitz, Bert F. "The City, The Factory, and Economic Growth." The American Economic Review 45, no. 2 (1955): 166-84. Accessed December 22, 2020. http://www.jstor.org/stable/1823550.
- Kenton, Will. “Heavy and Light Industry Defined: Fundamental Analysis of Industry Sectors.” Investopedia. Accessed December 22, 2020. https://www.investopedia.com/terms/h/
- Thompson, Francis Michael Longstreth. The rise of respectable society: a social history of Victorian Britain, 1830-1900. Harvard University Press, 1988.
- Taylor, Frederick Winslow. Scientific management. Routledge, 2004.
- Scholliers, Peter, and Vera Zamagni, eds. Labour's reward: real wages and economic change in 19th-and 20th-century Europe. Edward Elgar Publishing, 1995.
- Lee, Clive H. "The service sector, regional specialization, and economic growth in the Victorian economy." Journal of Historical Geography 10, no. 2 (1984): 139-155.
- Nayyar, Deepak. "Globalisation, history and development: a tale of two centuries." Cambridge journal of economics 30, no. 1 (2006): 137-159.
- Dautovic, G. “Automation and Job Loss Statistics in 2020-The Robots are Coming.” Fortunly. (2020): 1-13.
- Taulli, Tom. "RPA Foundations." In The Robotic Process Automation Handbook, pp. 1-25. Apress, Berkeley, CA, 2020.
- Lin, Yanliu. "E-urbanism: E-commerce, migration, and the transformation of Taobao villages in urban China." Cities 91 (2019): 202-212.
- Wang, Jing. “Taobao Villages Driving ‘Inclusive Growth’ in Rural China.” Alizila. (2019): 1-9.
- Lin, Juan and Ling Zhang. “E-Commerce, Taobao Villages and Regional Development in China .“ Geographical Review (2019): 1-25.
- Bansal, Ben. “Urban Manufacturing in Ota-Ku.” Economics Tokyo (2016): 1-6.
- Okuda, Koji and Makiko Uchida. “A Challenge From Japan.” Mitsubishi Materials (2018): 1-16.
- Unknown Author. “A Guide to Ota City Industries.” Ota City Industrial Promotion Organisation (2011): 1-19.
- Xu, Xun William, and Stephen T. Newman. "Making CNC machine tools more open, interoperable and intelligent—a review of the technologies." Computers in Industry 57, no. 2 (2006): 141-152.
- Lipson, Hod, and Melba Kurman. “Fabricated: The new world of 3D printing.” John Wiley & Sons, 2013.
- Varostis, Alkaios Bournias. “CNC Machining is More Accessible Than You May Think”. Manufacturing.net (2018): 1-12. https://www.manufacturing.net/industry40/article/13245730/cnc-machining-is-more-accessible-than-you-may-think
- Dameri, Renata Paola, and Camille Rosenthal-Sabroux, eds. Smart city: How to create public and economic value with high technology in urban space. Springer, 2014.
- Cooke, Philip, and Dafna Schwartz, eds. Creative regions: technology, culture and knowledge entrepreneurship. Routledge, 2008.